The Ultimate Guide to Die Cast Mold Makers
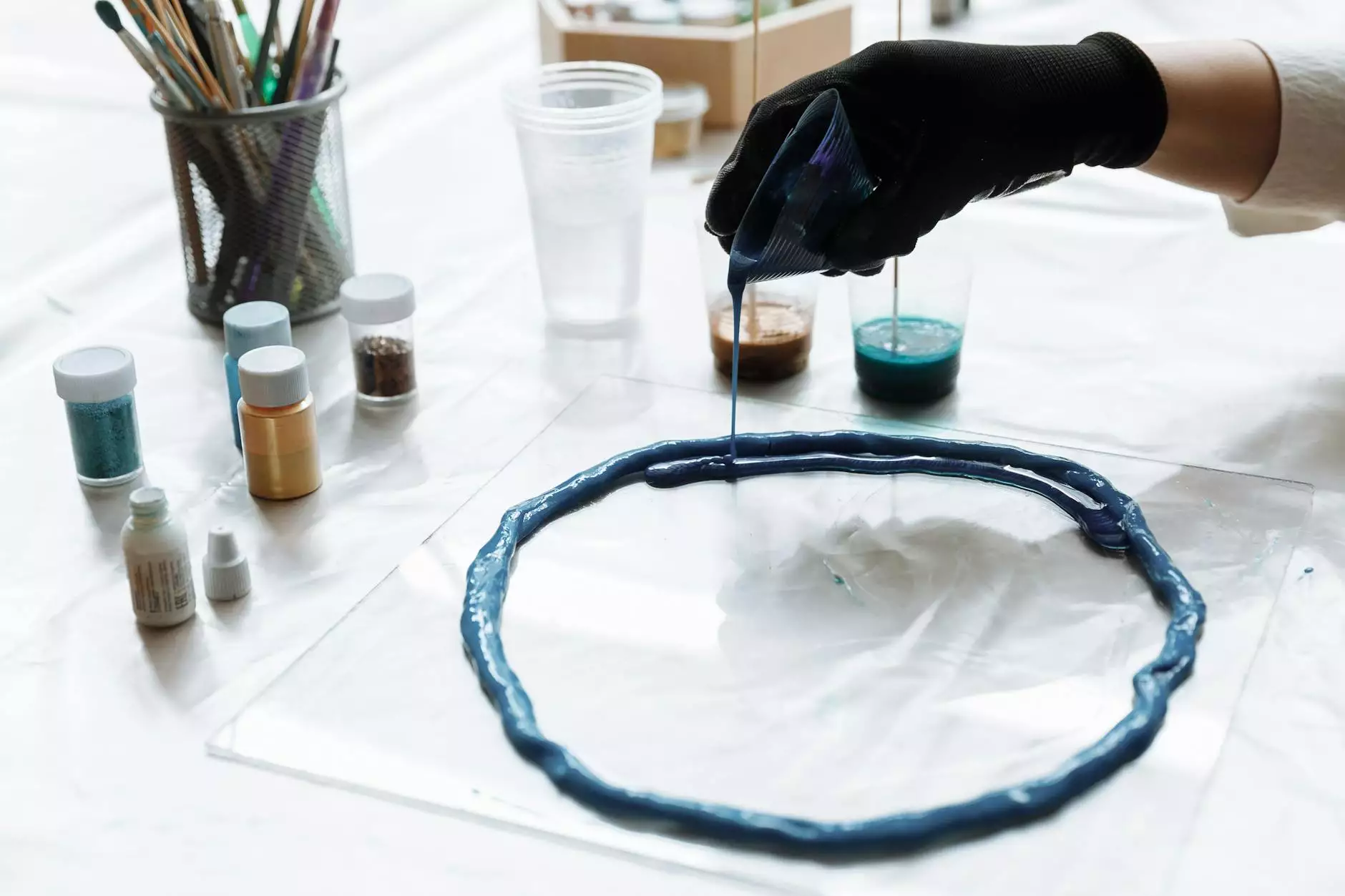
In the realm of manufacturing, especially in the metal fabrication industry, the role of die cast mold makers is pivotal. These artisans and engineers specialize in creating molds that enable the mass production of complex metal parts with precision and efficiency. Understanding their craft and the impact it has on various industries is essential for anyone looking to delve into the world of metalworking and fabrication.
What Are Die Cast Mold Makers?
Die cast mold makers are professionals skilled in designing and manufacturing molds used in the die casting process. Die casting is a method which involves forcing molten metal into a mold cavity under high pressure. This technique is favored for its ability to produce intricate shapes and fine details that are consistent in quality and dimension.
The Die Casting Process
The die casting process can be broken down into several critical stages:
- Mold Design: The first step involves creating a comprehensive mold design based on the desired product specifications.
- Mold Fabrication: Utilizing high-grade metals, mold makers fabricate the mold components with precision equipment.
- Melting and Pouring: The chosen metal is melted and then poured into the mold cavity.
- Cooling and Ejection: Once the metal cools and solidifies, the mold is opened, and the cast part is ejected.
- Finishing Processes: The final component may require additional processing, such as trimming, machining, or surface treatment.
The Importance of Quality in Mold Making
Quality control is paramount in the work of die cast mold makers. Every detail matters, as even minor imperfections can lead to significant failures in the final product. High-quality molds lead to:
- Reduced Costs: By ensuring accuracy, manufacturers reduce material waste and minimize the need for rework.
- Enhanced Production Speed: Quality molds allow for quicker cycles and faster product turnaround.
- Improved Product Consistency: Consistent mold quality translates into uniformity in the finished products.
- Longevity of Molds: Well-constructed molds have greater resistance to wear and tear, extending their lifespan.
Key Materials Used by Die Cast Mold Makers
The choice of materials in mold making is crucial, as the molds should withstand extreme conditions. Typically, die cast mold makers work with:
- Steel: The most common material due to its strength, durability, and ability to withstand high temperatures.
- Aluminum: Used for its lightweight properties and excellent thermal conductivity, often for prototypes.
- Copper Alloys: These materials excel in heat transfer, making them ideal for cooling channels in molds.
Technological Advances in Die Casting
The field of die casting has seen remarkable advancements due to emerging technologies:
3D Printing in Mold Design
3D printing allows polyjet technology to create complex mold designs that were previously challenging or impossible to achieve. This innovation not only speeds up the prototyping phase but also enables more intricate designs, leading to greater creativity in product development.
Computer-Aided Design (CAD)
The integration of CAD software has revolutionized the way die cast mold makers design molds. It enables precise modeling and simulation of the die casting process, reducing errors and enhancing design capabilities.
Applications of Die Cast Mold Making
The applications of die casting are vast and span numerous industries:
- Automotive Industry: Die casting is crucial in manufacturing components like engine blocks, transmission housings, and intricate brackets.
- Aerospace Sector: Components that require high precision and durability, such as turbine housings and structural parts, often utilize die casting.
- Consumer Electronics: The production of housings for devices like smartphones and laptops frequently employs die cast components.
- Medical Equipment: Components such as surgical instruments and housings for medical devices benefit from die casting technology.
Choosing the Right Die Cast Mold Maker
Selecting the right die cast mold maker for your project is crucial. Here are some factors to consider:
- Experience: Look for mold makers with a proven track record and extensive industry experience.
- Technology: Ensure they use advanced manufacturing technologies to deliver superior molds.
- Quality Assurance: Check their quality control processes to ensure consistent results.
- Customization: The ability to provide tailored solutions for your specific needs is a significant advantage.
The Future of Die Casting and Mold Making
The future of die cast mold makers looks promising as advancements in technology continue to shape the industry. Trends such as automation, increased use of sustainable materials, and improvements in robotic handling are setting the stage for even more efficient and cost-effective die casting processes.
Emphasis on Sustainability
With the growing emphasis on sustainability, integrating eco-friendly practices in mold making and die casting processes is becoming more important. This includes using recyclable materials and reducing emissions during production.
Conclusion
The significance of die cast mold makers in the manufacturing landscape cannot be overstated. Their expertise not only enhances product quality but also drives efficiency in production processes across various industries. As technology evolves, so too will the capabilities of these mold makers, ensuring that they remain integral to modern manufacturing.
For businesses seeking to maximize their manufacturing potential, investing in partnerships with high-quality die cast mold makers is essential. Companies like Deep Mould exemplify what it means to be at the forefront of this industry, providing comprehensive services and support that are vital for successful production.